Key Takeaways
The global COVID-19 pandemic, international conflicts, and other factors have led to significant supply chain issues affecting businesses across industries. Among the most pressing challenges faced by businesses reliant on fleets and heavy equipment is navigating the ongoing parts shortages. These problems are impacting operations of all sizes, but with effective maintenance planning you can mitigate their impact and keep your business running smoothly.
Table of Contents
- Understanding the Challenge
- What is a Maintenance Plan?
- Three Ways Digital maintenance Planning Helps Navigate parts Shortages
- Embracing Digital Maintenance Planning
Understanding the Challenge
The global business landscape has been grappling with unprecedented parts shortages, that have significantly affected the automotive and manufacturing industries. These shortages often lead to delayed maintenance schedules, pushing vehicles and equipment to operate beyond optimal conditions, increasing the risks of breakdowns and unplanned downtime. The impact is further compounded by restricted parts availability, which extends periods of vehicle downtime when reactive maintenance is needed. This ripple effect is felt across business operations, impacting productivity and profitability.
What is a Maintenance Plan?
An effective maintenance plan is the best way to address parts shortages, but what does this plan look like in practice? In essence, it's a strategic approach to managing the maintenance of equipment and vehicles. It involves setting maintenance schedules that ensure each asset receives timely servicing, inspections, and repairs. Proactively planning with this mindset helps minimise disruptions so you can create contingency plans to deal with parts shortages.
In the face of parts shortages, a well-structured maintenance plan is even more essential because it shifts the focus from reactive to proactive maintenance. This forward-thinking approach allows businesses to anticipate future needs, plan their parts inventory in advance and manage resources more efficiently.
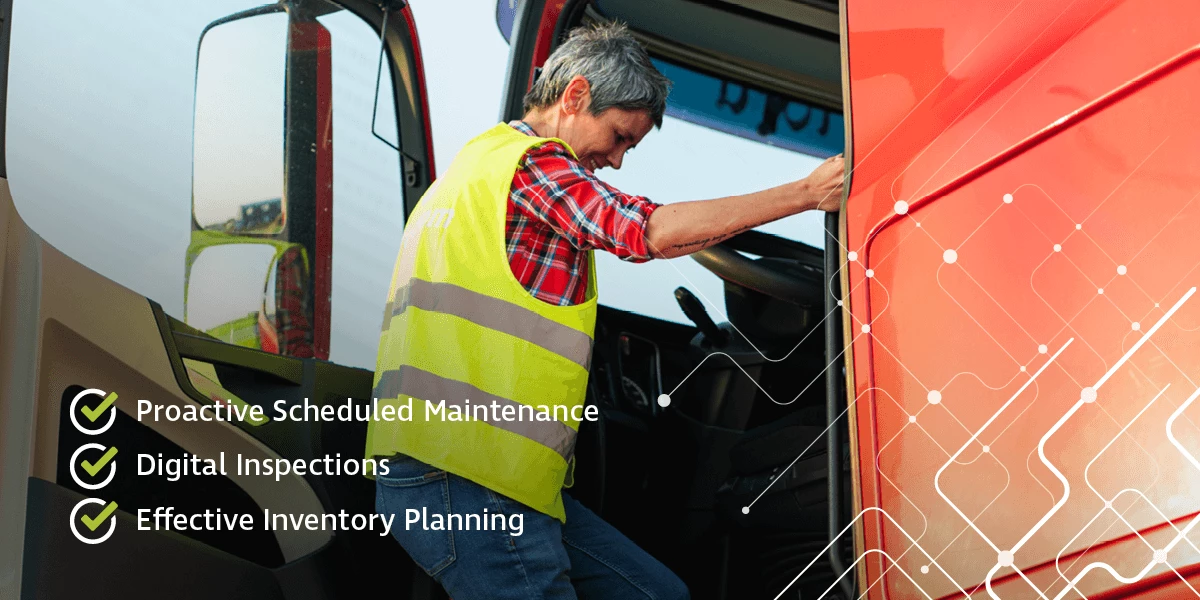
Three Ways Digital Maintenance Planning Helps Navigate Parts Shortages
Amid parts shortages, digital maintenance planning is a crucial tool for businesses. It offers a structured approach to handle the challenges posed by these shortages in three key areas.
1). Proactive Scheduled Maintenance
Digital maintenance planning tools revolutionise how businesses approach their maintenance schedule. By transitioning from a reactive to a proactive maintenance model, companies can significantly mitigate the impact of parts shortages. These tools allow for the automated scheduling of maintenance tasks based on real-time data such as engine hours, odometer readings, and historical maintenance records. This approach ensures that vehicles and equipment receive attention before issues escalate into costly repairs, reducing the vulnerability to parts availability.
2). Inspection Processes
By integrating digital inspection processes into a proactive maintenance schedule, fleet operators get real-time feedback on vehicle health, enabling them to resolve small issues before they become larger problems that require additional parts to resolve. A digitised inspection process also provides maintenance teams with data that enables them to plan inventory to cover the most common issues raised on failed inspections.
3). Optimised Inventory Management
One of the most vital aspects of maintenance planning is ensuring the availability of parts. Digital platforms help by providing visibility into future maintenance needs and providing data on frequently used parts. This enables maintenance teams to plan ahead and purchase parts in advance of future needs, reducing downtime due to extended maintenance periods.
Embracing Digital Maintenance Planning
Many fleet management platforms include the maintenance scheduling tools that are designed to help businesses streamline maintenance processes and provide visibility into maintenance activity. When assessing providers there are number of key items that you should be looking for, these include:
- Automated Maintenance Schedules. You will want a maintenance platform that offers the flexibility to run maintenance schedules of odometer readings, engine hours or set time periods. This will give you the flexibility to create schedules for a wide range of vehicles and equipment.
- Telematics Integration. This enables scheduled events to be automated based on data gathered through the telematics system, including odometer readings and engine hours.
- Inspection Application. Tools with a fully integrated inspection application enable drivers to easily complete checklists, inspection reports to be captured in real-time and work-orders to be automatically generated.
- Alerts and Reporting. Stay updated with immediate alerts for maintenance needs and service dates, allowing for proactive planning and management during parts shortages.
- Comprehensive Reporting. Gain a clear view of your fleet's health with TN360's detailed reports on maintenance activities to support decision-making.
These facets collectively form a powerful tool for businesses aiming to optimise their maintenance plan, tackle parts shortages, and achieve long-term fleet operational resilience. If you're looking to improve your maintenance processes, build your solution today and see how our fully integrated maintenance platform can help your business.
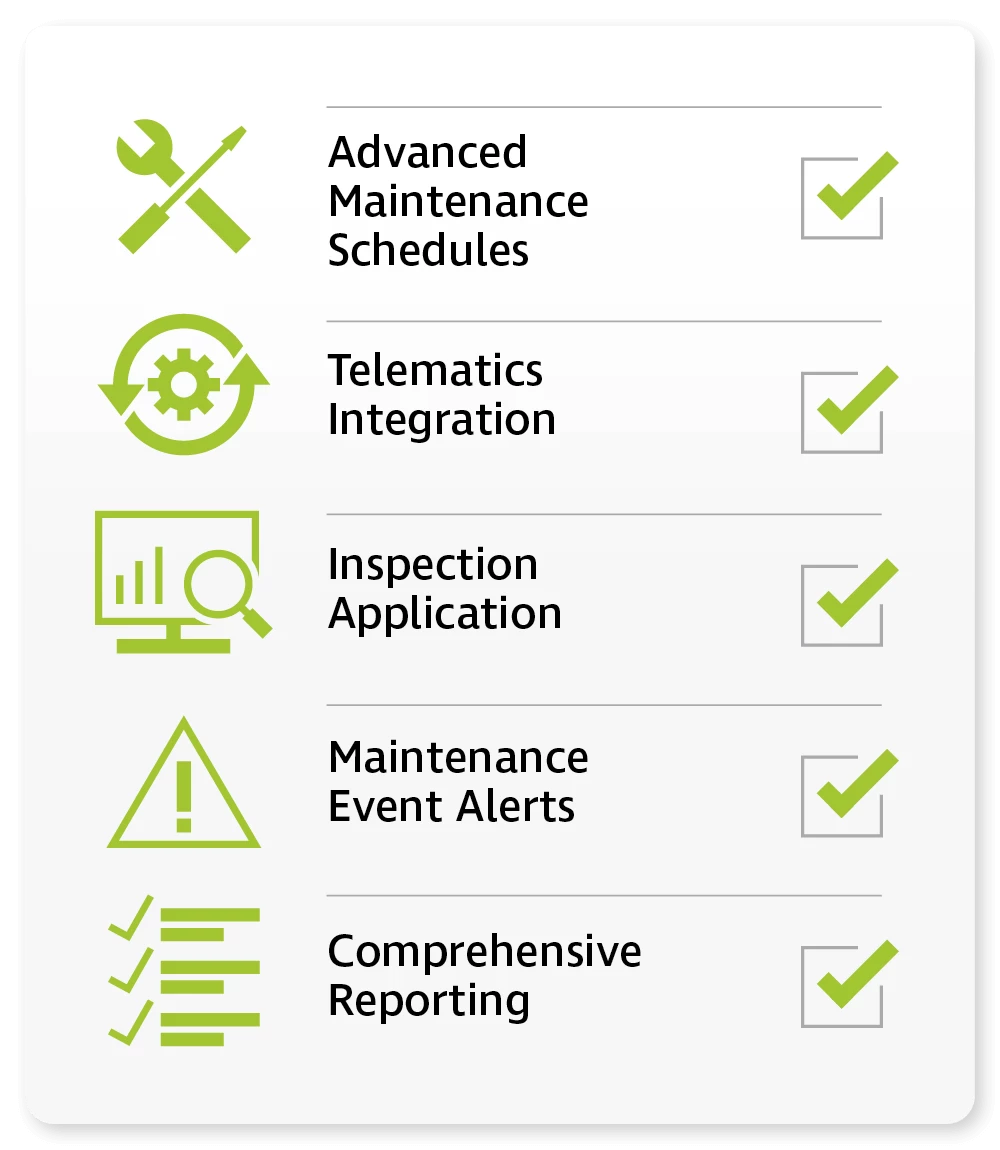